Are you looking at expanding your knowledge when it comes to supply chain and logistics? Are you aware of the basic, must-know concepts of the supply chain?
This article is an introduction to logistics and the supply chain, as well as the basic concepts that will expand your overall knowledge of the importance of logistics in business settings.
To start off, we’ll go over key business concepts used in logistics, and we’ll finish things up by breaking down more in-depth terms about the logistics and transportation system, which can be found in Part 2 of this article.
We hope that by the time you’ve finished reading, you’ll have a better understanding about the basic terms in logistics.
Shall we?
What are the ABC’s of logistics and supply chain management?
The ABC of logistics and supply chain refers to the classification of products or inventory based on their value and importance to the organization.
This classification system is used to help businesses prioritize the allocation of resources and make informed decisions about inventory management, transportation, and other logistics activities.
Let’s go over the three categories of the ABC classification system:
- A: High-value or high-priority items that are important to the business and require close management and attention. These items may have a high level of demand, a short shelf life, or other special characteristics that make them critical to the business.
- B: Moderate-value or moderate-priority items that are important to the business, but not as critical as A-items. These items may have a lower level of demand or longer shelf life, and may require less frequent monitoring and attention.
- C: Low-value or low-priority items that are less important to the business and can be managed with less attention and fewer resources. These items may have a low level of demand or a long shelf life, and may not require as much management or attention as A or B items.
The ABC classification system is a useful tool for businesses to prioritize the allocation of resources and make informed decisions about inventory management, transportation, and other logistics activities. By classifying products and inventory based on their value and importance, businesses can optimize their supply chain and logistics operations to ensure they’re meeting the needs of their customers efficiently and effectively.
What is logistics?
Logistics refers to the planning, organization, and management of the movement and storage of goods, services, and information from their production point, to the end consumer, which can be a final customer or a business (B2C or B2B).
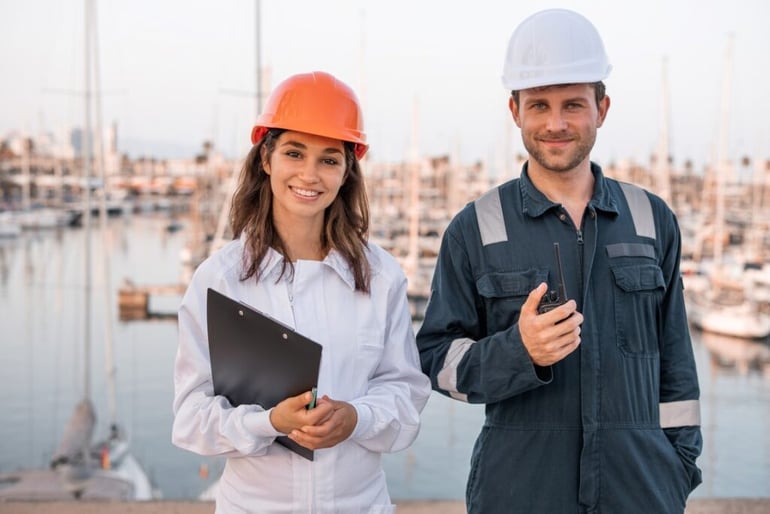
Its main function is coordinating and integrating various activities and functions across multiple locations, including transportation, warehousing, and distribution, to deliver goods and services to customers efficiently and effectively.
And supply chain management?
Supply chain management refers to the management of the flow of goods, services, and information from the point of origin to the point of consumption. Much like logistics, it works in coordinating and integrating most of the activities and functions involved in the production, handling, and distribution of goods and services, from the sourcing of raw materials to the delivery of finished products to customers.
What about business logistics management?
Business logistics management oversees the efficient and effective day-to-day activities that revolve around the production of finished goods and services within a company. It oversees the whole process that has to do with moving goods from one place to another, be that from a provider to a business (B2B), or from a business to a final customer.
The key takeaway here, is being able to manage all the processes involved in the above as a unified front, considering all the parties involved.
In practice, business logistics management may involve a range of activities, including:
- Sourcing and procurement: Identifying and sourcing the raw materials and components needed to produce goods and services.
- Production planning and control: Planning and coordinating the production of goods and services, including the scheduling of activities and the allocation of resources.
- Inventory management: Managing the flow of materials and finished goods in and out of the organization, which includes the tracking and optimization of inventory levels and storage.
- Transportation and distribution: It involves the planning and coordination of the movement and delivery of goods and services to customers, including the selection of transportation modes and routes, and the management of transportation and distribution networks.
- Customer service: Managing customer relationships and ensuring that customer needs are met in a timely and efficient manner, including the management of orders, returns, and complaints.
Overall, business logistics management involves the coordination and management of resources and activities to ensure that goods and services are delivered to customers in an efficient and effective manner. It requires a strong understanding of the organization's operations, as well as an ability to anticipate and respond to changes in demand and other factors that can impact the logistics process.
What’s the difference between inbound and outbound logistics?
Inbound logistics refers to the movement and storage of goods, services, and information from suppliers to the organization. It involves the coordination and management of resources and activities related to the receipt, handling, and storage of raw materials, components, and finished goods from suppliers and vendors.e
Outbound logistics, on the other hand, refers to the movement and storage of goods, services, and information from the organization to customers. It involves the coordination and management of resources and activities related to the distribution, transportation, and delivery of finished goods and services to customers, as well as managing returns and reverse logistics.
What role does transportation play in logistics?
Transportation refers to the movement of goods and people from one location to another, using various modes of transportation such as roads, railways, air, and water. It’s an essential part of logistics, since it involves the physical movement of goods and people from one place to another.
Logistics, on the other hand, refers to the planning, organization, and management of the movement and storage of goods, services, and information from an initial origin point, to its final delivery. It involves coordinating and integrating various activities and functions across multiple locations, including transportation, warehousing, and distribution, to deliver goods and services to customers quickly and on time.
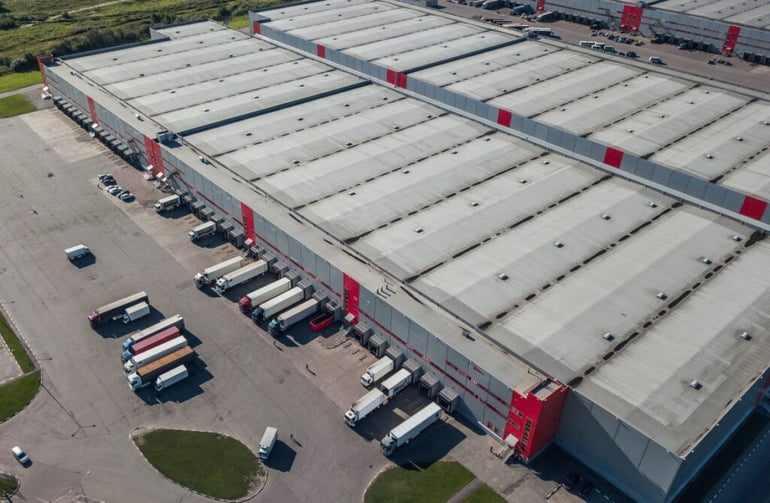
In short, transportation is a key component of logistics, but logistics encompasses much more than just the movement of goods and people. It involves the coordination and management of all the activities and resources necessary to deliver goods and services to customers in a timely and cost-effective manner.
SaaS TMS go hand in hand with transportation, since it has the ability to effectively manage a businesses transportation needs through a software.
For example, companies such as Drivin offer cloud-based solutions that help manage companies logistical operations.
What is the logistics cycle?
The logistics cycle refers to the series of activities that are involved in the planning, execution, and control of the movement and storage of goods, services, and information from the point of origin to the point of consumption, and includes the following stages:
- Planning: This involves identifying the needs of the customer and determining the most efficient and cost-effective way to meet those needs. This also requires having a full understanding of the transportation mode, the route, and the type of equipment and facilities that will be used.
- Execution: This encompasses the organization and coordination regarding the movement of goods and services, including the transportation, warehousing, and distribution of goods.
- Control: This revolves around monitoring and controlling the logistics process to ensure that it’s running smoothly and efficiently, and making any necessary adjustments to the plan in real-time.
- Documentation: This involves the creation and maintenance of records and documentation related to the logistics process, including shipping documents, customs documents, and other relevant documents.
- Feedback: This involves collecting and analyzing data on the performance of the logistics process, and using this information to make improvements and optimize future operations.
It's important to keep in mind that the logistics cycle is an ongoing process that oversees the coordination and management of resources and activities to ensure that goods and services are delivered to customers in a timely and cost-effective manner.
What is international logistics and global logistics?
International logistics refers to the process of planning, organizing, and managing the movement of goods, services, and information from one location to another on a global scale. This includes the coordination of transportation, warehousing, customs clearance, and other activities necessary to facilitate the movement of goods and services between countries.
On the other hand, global logistics refers to the management of the flow of goods, information, and other resources, between the origin and the destination in a globalized supply chain. It looks at coordinating and integrating various activities and functions across multiple locations, including transportation, warehousing, and distribution, to deliver goods and services to customers around the world.
Both international logistics and global logistics involve the management of resources and the coordination of activities across multiple locations, but international logistics specifically focuses on the movement of goods and services between countries, while global logistics encompasses the management of resources and activities on a global scale.
What are 1, 2, 3, 4 and 5PL?
1PL, 2PL, 3PL, 4PL, and 5PL are terms that are used to describe different types of logistics service providers. These terms refer to the level of involvement and responsibility that the logistics service provider has in the logistics process.
- 1PL refers to a company that provides logistics services using its own resources, such as its own trucks, warehouses, and staff.
- 2PL refers to a company that provides logistics services on behalf of another company, using a combination of the company's own resources and those of third-party providers.
- 3PL refers to a company that provides a range of logistics services to other companies, including transportation, warehousing, and distribution. 3PLs typically use a combination of their own resources and those of other providers to deliver these services.
- 4PL refers to a company that acts as a manager and coordinator of logistics services, working with multiple 3PLs and other service providers to create and manage a customized supply chain solution for a customer.
- 5PL refers to a company that provides logistics services while also integrating and managing the entire supply chain for a customer, including sourcing, production, and distribution.
These terms describe different levels of involvement and responsibility in the logistical process, with 1PL being the most basic level and 5PL being the most comprehensive and integrated level.
Keep reading here for part 2