In today's global economy, supply chain management is becoming increasingly complex due to the increasing number of parties involved, the greater distances between them, and the increasing speed at which goods and services need to be delivered.
As such, logistics professionals who are skilled in supply chain management are in high demand, as they’re able to help companies optimize their supply chains and achieve a competitive advantage.
This post is carrying on from the previous article regarding Logistics and Supply Chain ABC’s and Key Terms, Part 1
What is delivery route planning?
Delivery route planning refers to the process of determining the most efficient and cost-effective routes for delivering goods and services to customers.
It involves identifying the locations of customers and the quantities of goods and services that need to be delivered to each location, and determining the best route while scheduling deliveries to those locations.
Delivery route planning can be done manually or with the use of specialized software and technology. Manual route planning typically involves creating a map of the delivery area, identifying the locations of customers, and determining the most efficient routes based on factors such as distance, time, and traffic.
Specialized software and technology, on the other hand, can automate the route planning process by using algorithms to optimize routes based on a variety of factors, including distance, time, traffic, and customer preferences.
Delivery route planning is an important aspect of logistics and supply chain management, as it can help businesses optimize the movement of goods and services to customers, reduce costs, and improve customer satisfaction.
How important is route optimization software for logistics?
Route optimization software is a must-have tool for logistics and supply chain management, as it can help businesses optimize the movement of goods and services to customers, reduce costs, and improve customer satisfaction.
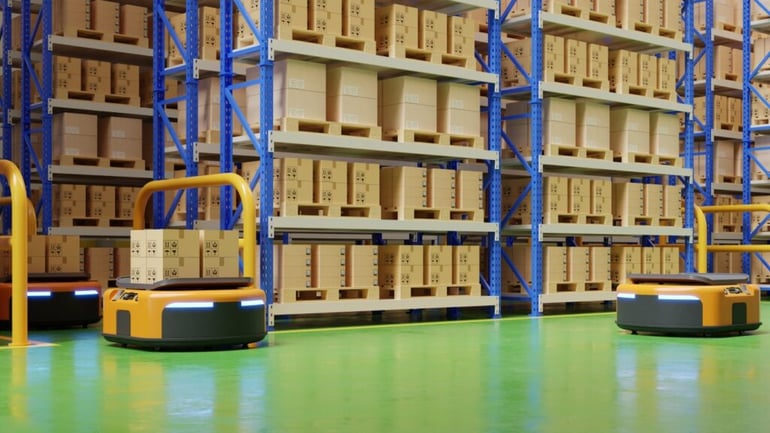
Route optimization software uses algorithms to analyze data on factors such as distance, time, traffic, and customer preferences to determine the most efficient and cost-effective routes for delivering goods and services, which can help businesses minimize travel time and distance, reducing fuel consumption and their operations’ carbon footprint.
In addition, route optimization software can also help businesses streamline their operations by reducing the need for manual route planning and enabling them to make real-time adjustments to routes as needed.
Overall, route optimization software is an important tool for logistics and supply chain management, as it can help businesses optimize their operations and improve the efficiency and effectiveness of their delivery processes.
What is a SaaS TMS?
TMS stands for Transportation Management System, and SaaS stands for Software as a Service. A SaaS TMS is a type of software that is delivered and accessed through the internet, rather than being installed on a local computer or server.
A SaaS TMS is a transportation management system that is delivered and accessed through the internet, rather than being installed on a local computer or server. It’s a type of software that’s designed to help businesses manage and optimize their transportation and logistics operations, including the planning and scheduling of shipments, the selection of carriers and modes of transportation, and the tracking and monitoring of shipments and deliveries.
SaaS TMS solutions are typically subscription-based, with users paying a monthly or annual fee to access the software. They offer a range of benefits, including the ability to access the software from any location with an internet connection, and the ability to scale the software up or down based on the needs of the business.
Companies like Drivin offer SaaS TMS solutions for businesses that need to manage and optimize their transportation and logistics operations, and want to access a transportation management system through the internet and in real-time, rather than installing it on a local computer or server.
Logistics tracking and it’s benefits
Logistics tracking refers to the process of monitoring and recording the movement and location of goods, services, and information during the logistics process.
There are several benefits to logistics tracking:
- Improved efficiency: By tracking the movement of goods and services, businesses can optimize their logistics operations and reduce the risk of delays or errors.
- Reduced costs: Logistics tracking can help businesses reduce costs by minimizing waste and inefficiencies in the logistics process.
- Improved customer satisfaction: By providing customers with real-time visibility into the location and status of their orders, businesses can improve customer satisfaction and build stronger relationships.
- Enhanced security: Logistics tracking can help businesses improve the security of their supply chain by enabling them to track and monitor the movement of goods and services and detect any potential issues or risks.
- Increased transparency: Logistics tracking can help businesses improve transparency in their supply chain by providing visibility into the movement of goods and services and enabling them to identify potential issues or bottlenecks.
What is reverse logistics?
Unlike regular logistics, reverse logistics refers to the process of managing the movement of goods and materials from the end consumer to the production point. It involves the coordination and management of resources and activities related to the return, repair, refurbishment, disposal, or recycling of goods and materials.
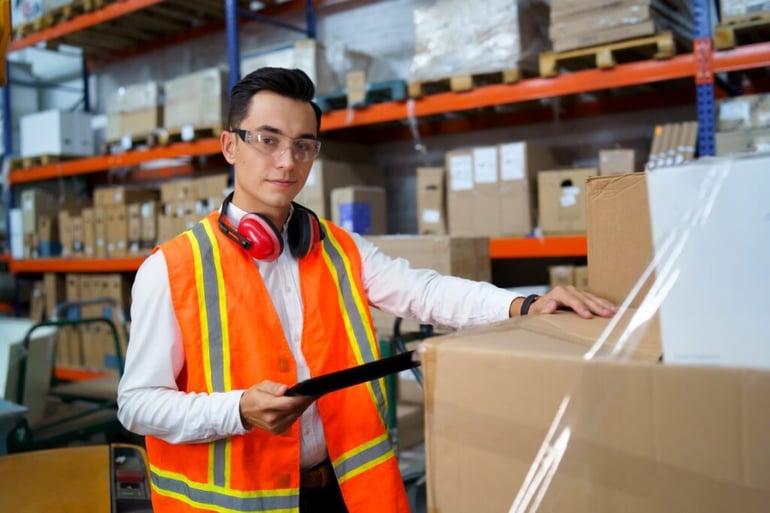
Technology plays a significant role in reverse logistics, as it can help businesses automate and optimize the reverse logistics process, and improve the efficiency and effectiveness of their operations. Some examples of how technology is used in reverse logistics include:
- Tracking and tracing: Technology can be used to track and trace the movement of goods and materials through the reverse logistics process, enabling businesses to monitor the progress of returns and repairs and identify any bottlenecks or issues.
- Inventory management: Technology can be used to manage inventory levels and optimize the flow of goods and materials through the reverse logistics process, helping businesses to minimize waste and reduce costs.
- Customer service: Technology can be used to improve customer service in the reverse logistics process, by enabling businesses to manage orders, returns, and complaints more efficiently and effectively.
- Data analysis: Technology can be used to analyze data on reverse logistics activities, helping businesses to identify trends and patterns and make informed decisions about the management of returns and repairs.
Overall, technology plays a key role in the reverse logistics process, helping businesses to automate and optimize their operations, improve efficiency and effectiveness, and make informed decisions about the management of returns and repairs.
What’s the last mile, and what can we expect for the following year?
Last mile refers to the final leg of the transportation of goods and services from a distribution center or fulfillment center to the end customer. It is the portion of the supply chain that involves the delivery of goods and services to the customer's doorstep or place of business.
The last mile is typically considered one of the most complex and expensive parts of the supply chain, as it involves navigating through urban areas, traffic congestion, and other challenges. As such, it is an area of focus for many businesses looking to improve the efficiency and effectiveness of their supply chain operations.
In recent years, there has been a growing trend towards the use of technology and innovative solutions to improve the last mile. Some examples of how the last mile is changing include:
- The use of autonomous vehicles and drones: These technologies are being explored as a way to reduce the cost and complexity of last mile deliveries, by enabling goods and services to be delivered directly to the customer without the need for a human driver.
- The use of urban fulfillment centers: Urban fulfillment centers are smaller, more densely located warehouses that are designed to support last mile deliveries in urban areas. They can help reduce the distance and time required for last mile deliveries, and improve the efficiency of the supply chain.
- The use of alternative delivery models: Businesses are exploring a range of alternative delivery models, such as crowdsourced delivery, to improve the efficiency and cost-effectiveness of last mile deliveries.
Overall, the last mile is an important and evolving part of the supply chain, and businesses are continuously seeking ways to improve the efficiency and effectiveness of last mile deliveries through the use of technology and innovative solutions.
What are the most common KPI in logistics?
KPI stands for Key Performance Indicator, and is a measure used to evaluate the performance of a business or process. In logistics, common KPIs include:
- On-time delivery: The percentage of orders that are delivered on time, as specified by the customer or agreed upon in the contract.
- Order accuracy: The percentage of orders that are fulfilled correctly, without errors or discrepancies.
- Inventory accuracy: The percentage of inventory records that accurately reflect the actual quantity of goods on hand.
- Order processing time: The time it takes to process and fulfill an order, from the time the order is received to the time it is shipped.
- Transportation cost: The total cost of transportation, including fuel, labor, and other expenses.
- Customer satisfaction: The level of satisfaction of customers with the quality of service and delivery performance.
- Damage rate: The percentage of orders that are damaged during transportation or handling.
These are some of the most common KPIs used in logistics to evaluate the performance of logistics operations and identify areas for improvement.
If you or your company is looking at incorporating technology driven software to optimize and make your operation more agile, feel free to get in touch to get a free demo at Drivin.
Categories
- Data Management
- Fleet Management
- Last Mile
- Logistics
- Omnichannel
- Route Optimization
- Route Planning
- Supply Chain
- Sustainable Logistics
- TMS
- Trends & news
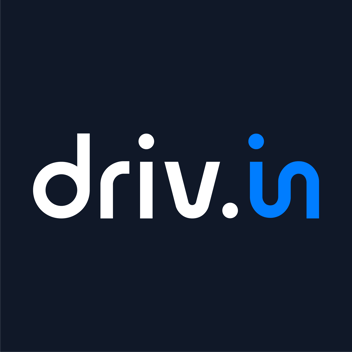
Technology, Security and Sustainability: What to look for in a TMS
In the fast-paced business environment, having an edge in logistics can make or break customer...